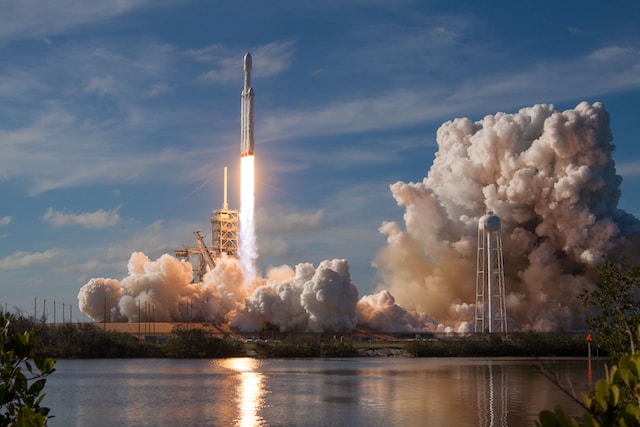
Aerospace bearings need to withstand extremely high temperatures. They also need to be corrosion-resistant and retain strength and hardness. The materials used in aerospace bearings have become increasingly specialized to meet the demands of these extreme environments.
Safety First
Customized bearings are often more expensive than stock bearings, but they offer many benefits that drive down operating costs and minimize downtime. However, a decision to use a specific bearing solution should be made after analyzing the whole life cost of the bearing. Aerospace applications such as gimbal mounts, medical scanners, radar platforms, and missile tracking systems require precision, space tightness, and absolute load capacity. They typically need thin section bearings to achieve these requirements. Using advanced high-technology features such as deep nitrocarburization can significantly extend the fatigue life of a bearing. The manufacturing process of custom bearings must meet strict quality and production standards, just like the special design requirements Danbury, CT. This is to ensure that a superior-quality product is delivered. This is achieved through materials that have been traced from the molten stage through the use of specialist coating and precision manufacture processes.
Reduced Risk of Injuries
Properly installing high-quality custom bearings can go a long way toward keeping you and your equipment out of harm’s way. Properly matched, lubricated, and installed with care will save you money in the long run and keep you and your crew safe and healthy on the ground and in the air. The most important consideration is identifying the correct bearing for your application. The best way to do this is to ask your bearing supplier for a free, no-obligation quote. Then you can be sure you’re getting the best price possible and a product that will perform just as well in the field as in the shop.
Reduced Downtime
As with any equipment, excessive load, vibration, and force can wear out a bearing long before it should. Often, these failures can be avoided by properly installing custom bearings to the OEM’s specifications. An excellent place to start is by evaluating the life of your existing bearings. Using a loading analysis formula, you can convert all your bearing loads to an equivalent radial load Pe and calculate each bearing’s “rated” fatigue life under that load. This is a critical step because it lets you make more informed decisions about which custom bearings are best for your application. The results can help you avoid downtime and costly repairs. It also allows you to identify any problems that must be addressed before they cause damage and premature bearing failure.
Increased Productivity
The aerospace industry has a long history of utilizing custom bearings to ensure safety in designing, manufacturing, and installing aircraft components. These parts must meet strict specifications and withstand the harshest environments while maintaining high performance. Unlike off-the-shelf or stock bearings, which are designed to be mass-produced, custom bearings can reduce costs by optimizing the materials, heat treatment, clearances, and installation tolerances. This increases the efficiency of the overall design and reduces cost in the long run, which can help to increase productivity.